I rivestimenti ottici vengono utilizzati per migliorare le proprietà di trasmissione, riflessione o polarizzazione di un componente ottico. A titolo di esempio, una superficie in vetro con un opportuno trattatamento antiriflesso può arrivare a riflettere meno dello 0,1% della luce incidente, contro il 4% della stessa superficie non trattata [1].
Un rivestimento ottico è composto da una combinazione di layer sottili di diversi materiali quali ossidi, metalli o terre rare. Le prestazioni di un rivestimento dipendono dal numero di strati, dal loro spessore e dalla differenza di indice di rifrazione tra un layer e il successivo.
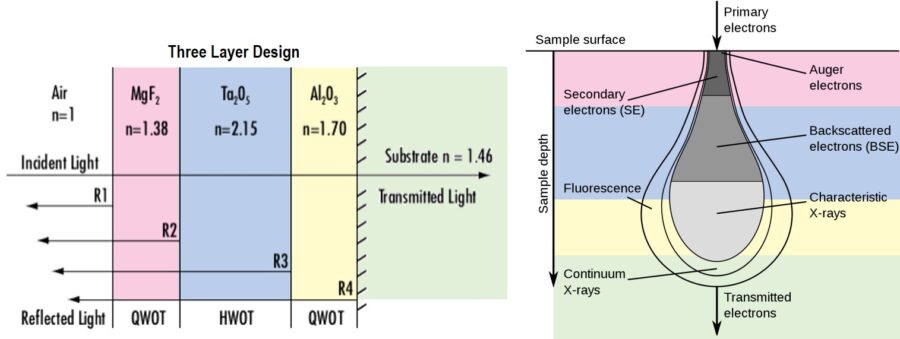
Fig. 1B – Rappresentazione del volume di interazione del fascio elettronico nel campione di coating antiriflesso.
I rivestimenti ottici a film sottile vengono in genere creati depositando strati sottili alternati costituiti da materiali dielettrici e metallici, come ad esempio pentossido di tantalio (Ta2O5), ossido di alluminio (Al2O3) o ossido di afnio (HfO2). Per indurre gli effetti di interferenza desiderati (massima trasmissione o massima riflessione), si depositano spessori ottici tipicamente di λ/4 (QWOT) o λ/2 (HWOT), dove λ è la lunghezza d’onda della luce utilizzata nell’applicazione di interesse, alternando un materiale ad alto indice di rifrazione ad uno a basso indice (Fig.1A). I rivestimenti ottici sono progettati per migliorare le prestazioni di un componente ottico per uno specifico angolo di incidenza e una determinata polarizzazione della luce (s, p oppure random). L’uso del rivestimento con un angolo di incidenza o una polarizzazione diversi da quelli per cui è stato progettato comporterà una perdita significativa delle sue funzioni.
È dunque evidente quanto sia di fondamentale importanza il controllo degli strati depositati, e così pure il fatto che in un’applicazione come questa la caratterizzazione dei layer non può essere eseguita con metodi distruttivi.
Ma niente paura, ci viene in soccorso il SEM, che grazie ai dati raccolti con il detector EDS, è in grado di confermare o smentire la composizione e gli spessori stimati per i layer che costituiscono il nostro campione di coating.
Grazie ad uno specifico tool del software di analisi EDS, è possibile sfruttare il volume di interazione del fascio di elettroni con il campione (Fig. 1B) per ottenere informazioni sullo spessore e sulla composizione degli strati sottili al suo interno. Tensioni di accelerazione diverse (1-30 kV) possono essere utilizzate per penetrare più o meno in profondità nel campione e caratterizzare più strati fino a uno spessore totale di 2-4.5 µm (a seconda della composizione).
Il primo step consiste nel creare un modello del campione che descriva i layer che lo compongono: elementi presenti, spessore nominale, densità e ordine degli strati (composizione e spessore possono essere definiti fissi o sconosciuti).
L’utente acquisisce quindi vari spettri EDS dal campione stratificato: il volume di interazione del fascio elettronico si estende all’interno del campione attraverso la struttura a strati, provocando la generazione di raggi X dai layer a diversa composizione.
Il modello creato nel primo step viene infine confrontato con gli spettri acquisiti e l’algoritmo ottimizza i risultati in modo iterativo per ottenere la migliore corrispondenza tra il modello e lo spettro del campione acquisito.
Per ottenere risultati affidabili è bene acquisire spettri con un elevato process time ed un buon numero di conteggi, ed è sempre raccomandato eseguire per prima cosa le routine di calibrazione e beam measurement impostando le stesse condizioni sperimentali che verranno utilizzate al SEM per l’acquisizione degli spettri EDS sul campione.
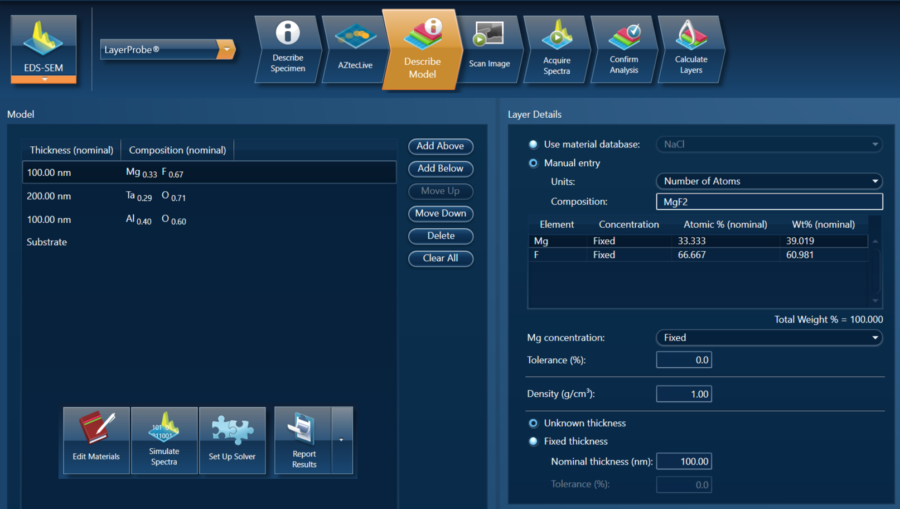