Il rame costituisce una delle aree più promettenti della stampa 3D in metallo in diversi settori, dai motori elettrici ai dissipatori di calore. In precedenza, la stampa 3D con il rame rappresentava una vera e propria sfida, a causa della riflettività del metallo e dell’elevata conducibilità termica, ma i progressi nelle stampanti e nei materiali hanno ampiamente superato queste prime sfide.
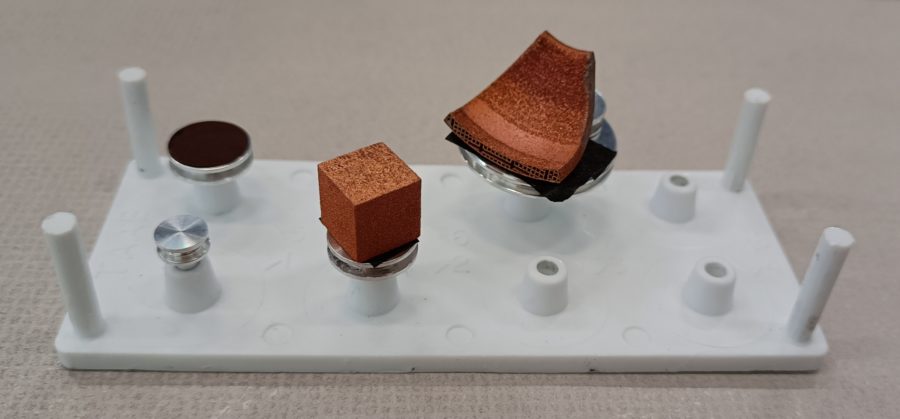
Oggi, i sistemi di propulsione in rame stampati in 3D inviano razzi nello spazio, i dissipatori di calore in rame stampati in 3D mantengono raffreddate le CPU e le bobine di rame stampate in 3D aumentano le prestazioni dei motori elettrici.
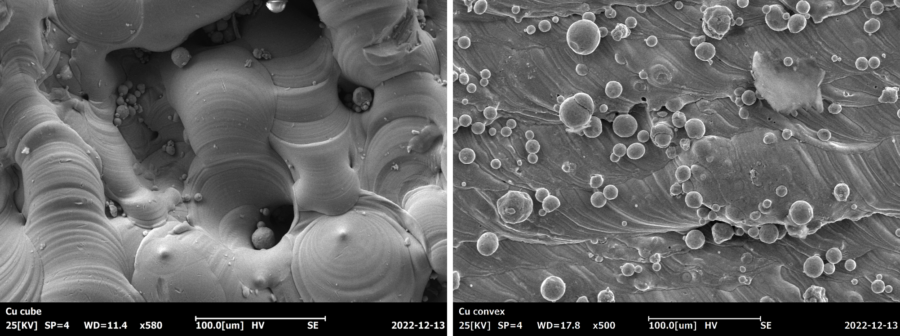
La domanda di parti complesse in rame sta crescendo poiché la stampa 3D apre ancora più applicazioni e possibilità per questo metallo. La stampa 3D (nota anche Additive Manufacturing) consente la produzione di forme eccezionalmente complesse, piccoli dettagli, strutture interne e riempimenti reticolari non possibili con nessun altro metodo di produzione in metallo. Queste caratteristiche permettono di ridurre il peso, aumentare l’efficienza e ridurre i tempi di produzione e assemblaggio, poiché gli assiemi multiparte possono essere stampati in 3D come una singola unità. La stampa 3D consente quindi una produzione più efficiente di questo metallo relativamente costoso, riducendo gli sprechi e utilizzando solo la quantità di materiale necessaria per ciascuna parte. Per le aziende interessate alla stampa 3D in rame, la riduzione dei costi delle materie prime è fondamentale. Così come lo è il controllo qualità sulle materie prime in ingresso, dalla composizione % della lega (Fig. 3) alla granulometria della polvere (Fig. 4).
La fusione a letto di polvere è uno dei metodi di stampa 3D in metallo più diffusi e diversi produttori di stampanti hanno recentemente introdotto il rame nel loro elenco di materiali stampabili. La fusione a letto di polvere è una tecnologia di stampa 3D che utilizza una fonte di calore, generalmente un fascio laser, per sinterizzare o fondere insieme particelle di materiale atomizzate. Come altri processi di fabbricazione additiva, ciò avviene tramite sovrapposizione di strati realizzati singolarmente fino a completamento del pezzo. Le due principali tecniche di fusione a letto di polvere per la stampa 3D in rame sono la DMLS (Direct Metal Laser Sintering) e l’EBM (Electron Beam Melting).
La famiglia del rame comprende le leghe Cu, CuCP e CuCrZr, impiegate a seconda dell’applicazione per cui il pezzo è stampato. La lega CuCrZr, ad esempio, presenta un’ottima combinazione di conduttività elettrica e termica unita a buone proprietà meccaniche. L’aggiunta di zirconio al rame-cromo migliora la resistenza al creep alle alte temperature di esercizio e riduce l’adesione degli elettrodi al pezzo durante la saldatura a punti di materiali zincati o rivestiti. La composizione della lega deve rispettare i valori dichiarati nelle schede tecniche (in genere il contenuto di Cromo è compreso tra 0.50 e 1.50% e il contenuto di Zirconio tra 0.02 e 0.20%), e può essere verificata mediante analisi SEM-EDS sulla polvere depositata su stub (Fig. 3).
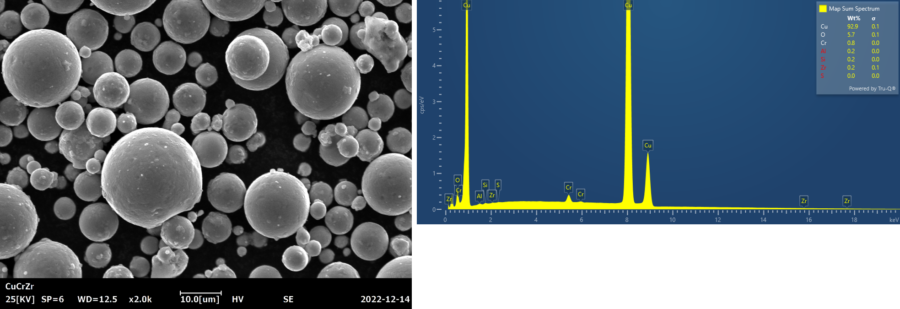
Oltre alla composizione chimica e al contenuto di ossigeno, anche altri parametri quali la distribuzione granulometrica delle particelle e la rotondità (fattore di forma), influenzano gli indici di prestazione delle parti stampate in 3D.
La corretta dimensione delle particelle di polvere da utilizzare va scelta in base al tipo di stampante: per le stampanti che impiegano un laser come fonte di energia, grazie al loro punto di messa a fuoco molto preciso e alla relativa facilità con cui possono fondere polveri fini, sono adatte polveri di dimensioni inferiori ai 50 μm. Per stampanti che utilizzano la tecnologia con plasma, invece, si utilizza in genere una polvere più grossolana (fino a 100 μm).
La rotondità rappresenta quanto la forma della particella è vicina a quella di una sfera (valore compreso tra 0 e 1), e influisce sulla fluidità, vale a dire la capacità della polvere metallica di scorrere attraverso un ugello. In generale, maggiore è il valore della rotondità, migliore è la scorrevolezza delle particelle di polvere, e più facile è controllare la deposizione e l’alimentazione della polvere durante la stampa 3D e quindi ottenere parti con una qualità di stampa superiore.
Grazie al software a corredo del SEM, è possibile misurare sia il diametro medio che il fattore di forma delle particelle di polvere. Dopo aver acquisito l’immagine SE o BSE di un’area a medio-basso ingrandimento, il software è in grado di calcolare la distribuzione granulometrica delle particelle, separando quelle molto vicine ed escludendo (come nell’esempio riportato in Fig. 4) quelle particelle che si trovano ai margini dell’area di osservazione e che quindi non sono visibili per intero. Con questi accorgimenti si evita di alterare la statistica delle misure e si ottengono dati maggiormente veritieri.
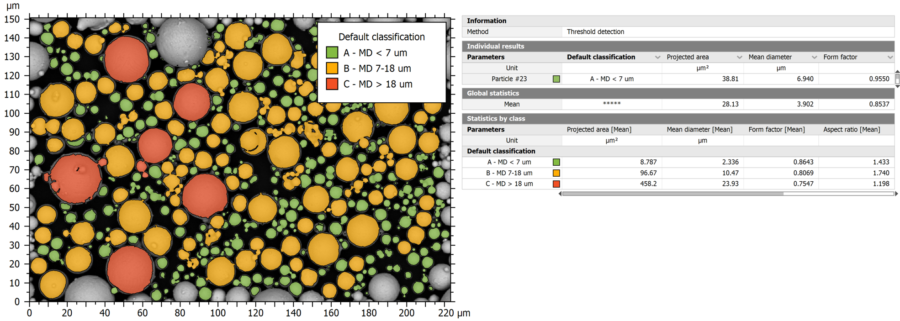